Meine Funktion: Ich war der verantwortliche Engineering Manager
Situation:
In Südafrika hatten wir eine neue Tochtergesellschaft erworben. Die Mitarbeiter waren kompetent, motiviert und das Qualitätsniveau wurde als “akzeptabel” eingestuft, lag aber deutlich unter dem, was die Kunden heute erwarten.
Ein riesiges Problem war, dass Prozesse weder standardisiert noch dokumentiert waren. Jeder Einzelne ging eine Aufgabe etwas anders an und arbeitete nach seinem eigenen “Standard”. Der extrem hohe Anteil an Mitarbeitern, die schon sehr lange in der Firma waren, verschärfte das Problem zusätzlich, da jeder sicher war, “die beste Methode zu kennen”.
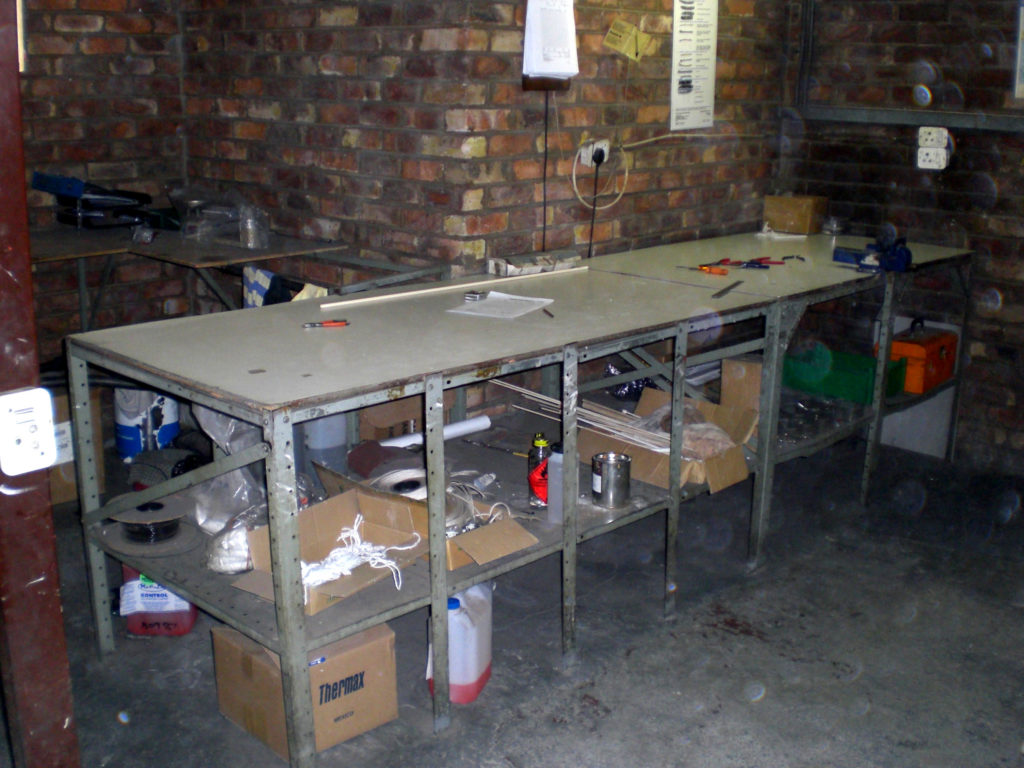
Die Ausrüstung und die Werkzeuge waren einfach und es gab keine “Qualitätsstandard” und in den Produktionsabläufen keine Standardvorgaben. Der eine konnte z.B. einen gewissen Druck auf das Produkt ausüben, ein Kollege einen anderen. Einer füllte etwas mehr Flüssigkeit ein, ein Kollege etwas weniger.
Eine interne Qualitätskontrolle versuchte, Fehler “aufzufangen”, beschränkte sich jedoch auf Funktionstests und Sichtprüfung. Doch keine davon konnte die “eingebauten Fehler” erkennen.
Lösung
Der erste Schritt bestand darin, die Prozesse zu dokumentieren und einen Konsens darüber zu erzielen, welcher Prozess, welche Methode und welcher Parameter der optimale war. Dies erforderte Mitarbeitergesprächen vor Ort, sowohl in Südafrika als auch in Europa. Es folgten moderierte Diskussionen, um sich zu einigen, wo unterschiedliche Meinungen bestanden (und es gab viele verschiedene Meinungen).
Als nächstes haben wir basierend auf dem Input der Mitarbeiter und den Ideen junger Ingenieure einen optimalen Prozessablauf und Produktionsparameter entworfen. Diese wurden dokumentiert und zur Grundlage der Produktion. Diese “roten Bücher” waren die Produktions-Bibel, dienten der Schulung neuer Mitarbeiter und zur Klärung bei weniger üblichen Prozessen.
Stücklisten wurden standardisiert und automatisch für jedes Produkt in Abhängigkeit von den bestellten Optionen generiert.
Neue Produktionsanlagen wurden eingeführt und soweit möglich so konzipiert, dass Qualität “eingebaut” wurde.
- z.B. ein voreingestellter Elektroschrauber sorgte dafür, dass jede Schraube mit einem konstanten Drehmoment angezogen wurde,
- ein automatisches Programmiergerät stellte die vom Kunden benötigten Parameter ohne manuelles Eingreifen ein,
- ein Laser druckte das richtige Typenschild mit allen erforderlichen Parametern.
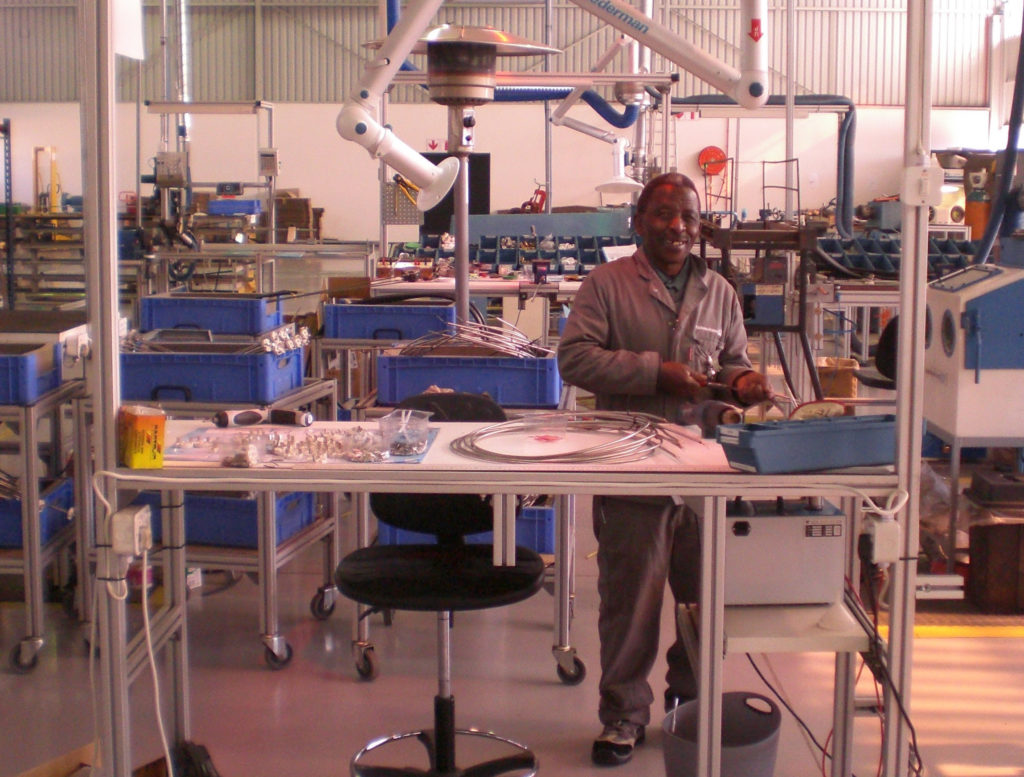
Die Qualität und die Produktivität stiegen immens, was vor allem zu einer verbesserten Kundenzufriedenheit führte.